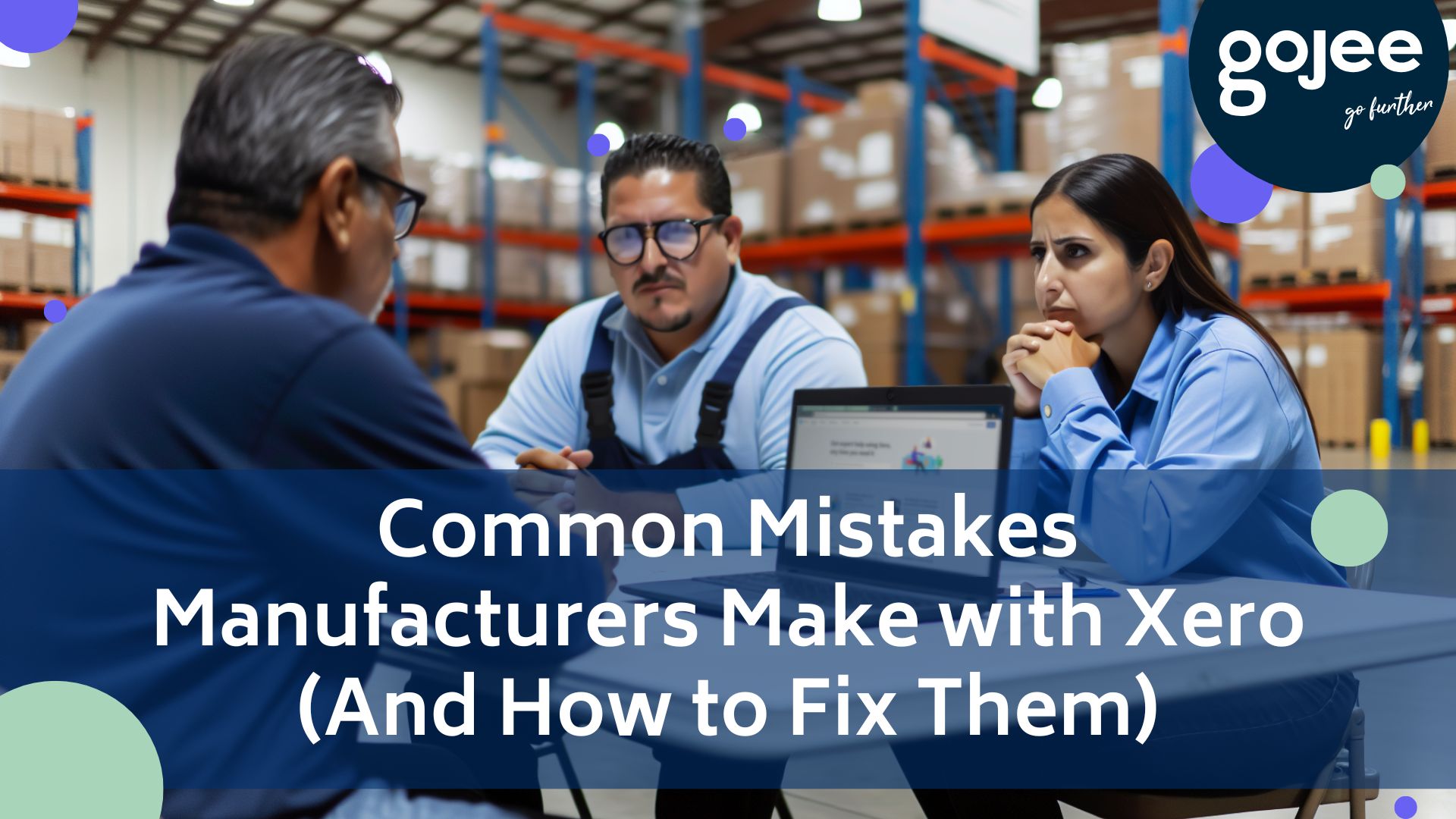
Common Mistakes Manufacturers Make with Xero (And How to Fix Them)
WE ALL KNOW IT – Managing raw materials, labour, equipment, and production costs can get overwhelming, especially when you’re trying to keep everything aligned with your finances. Xero accounting software can help simplify things—but many manufacturers miss out by not setting it up to fit their needs.
Let’s talk about five common mistakes manufacturers make with Xero—and how you can fix them.
1. Not Setting Up a Custom Chart of Accounts
Manufacturers often use Xero’s default accounts, which don’t really fit what they need. This can make tracking costs confusing.
The Solution: Create a chart of accounts that matches your production process. For example:
- Raw Materials for everything you buy to make your products.
- Work-in-Progress (WIP) for products still being made.
- Finished Goods for completed products.
- Manufacturing Overhead for things like machine maintenance and utilities.
This makes it easier to see where your money’s going and what stage it’s in.
Pro Tip: Use Xero’s tracking categories to keep an eye on different product lines or departments.
2. Forgetting to Track Labour Costs in Jobs
Labour is a huge cost in manufacturing, but many forget to assign these costs to specific jobs, making it hard to know which jobs are actually profitable.
The Solution: Use Xero’s timesheet feature to track labour costs by job. This way, every hour worked is linked to the right job, and you can see how labour is affecting your profit.
Pro Tip: To automate time tracking and save double data entry, try using Gojee to easily assign payroll costs to jobs, so you can really drill down into the numbers. Other tools like WorkflowMax also have features to assist this process.
3. Not Using Xero’s Inventory Tools to Their Full Potential
Manufacturers often stick to basic inventory tracking, which can lead to stock shortages or overstocking—both of which are costly.
The Solution: Xero has basic tools for tracking inventory, but if your supply chain is complex, you’ll need more than the basics. Gojee adds advanced features like goods receival, batch tracking, managing stock across multiple locations, and setting reorder points.
Pro Tip: With Gojee, you get real-time updates on stock levels, so you know exactly when to reorder and where your stock is, saving time and money.
4. Not Tracking Job Costs in Real Time
Waiting until the end of the month to check job costs means you’re often too late to fix any issues.
The Solution: You can use Xero Projects to assign costs (labour, materials, overhead) to specific jobs. But for real-time insights, Gojee can show you job costs as they happen, so you can make changes before costs get out of control.
Pro Tip: Gojee’s job level reporting can help you see which jobs are profitable and areas where you might need to cut costs or quote higher for the next job.
5. Not Integrating Xero with Other Tools
Many manufacturers treat Xero as a standalone tool, which means a lot of manual data entry and mistakes.
The Solution: Integrate Xero with other systems like payroll, scheduling and inventory tools to get the most out of Xero.
Pro Tip: Gojee is an all in one solution built for Xero which makes it easy to sync everything up so your data flows smoothly between platforms, cutting down on manual entry and errors. Check your current tools and see how seamlessly they work with Xero to save time and keep things running smoothly.
Manufacturing is already complicated. Your accounting software doesn’t have to be. By avoiding these mistakes and using Xero (and Gojee) to its full potential, you can streamline your processes, save money, and get better control over your finances.
Fix These Mistakes and Move Forward
Don’t let these common mistakes hold you back. Our free Xero Guide for Manufacturers gives you simple steps to streamline job costing, manage inventory better, and help you run your business smoothly.
Ready for the Next Step?
Take things further with a free trial of Gojee! Simplify job management, track costs effortlessly, and get real-time updates on your inventory – all in one place.